玻纖熱壓機的主要工藝——熱壓成型工藝
鑫臺銘玻纖熱壓機的關鍵工藝——熱壓成型工藝:---鑫臺銘提供。鑫臺銘---新智造走向世界!致力于3C電子、新能源、新材料產品成型及生產工藝解決方案。
玻纖板作為一種智能終端產品的外觀材料,具有多種優勢。它的密度低,強度高,不易變形,具有良好的抗摔性能,并且不必須使用保護殼。同時,玻纖及其布料作為常用的材料,具備成本低廉的特點。在智能設備的外殼設計中,玻纖能夠提供輕盈、薄型、硬質、易塑形以及低介電常數等優點,這使得它相比復合材料和玻璃蓋板能夠實現更輕薄的設計。
鑫臺銘開發了專門用于新材料碳纖、玻纖、復合材料的熱壓成型設備,設備壓力有100T-500T等不同規格。主要應用于手機后蓋、VR/AR智能穿戴、頭盔、無人機零部件、氣凝膠隔熱墊等碳纖、玻纖輕量化行業產品及航空航天、汽車制造、醫療器械、建筑建材、體育器材、消費電子、新能源等多個領域。
碳纖維熱壓成型機是一種專門用于新材料碳纖、玻纖復合材料的熱壓成型設備。該機采用熱壓技術,通過高溫、高壓將碳纖維和樹脂基體復合,使其具有優異的力學性能和輕量化特點。
熱壓成型機是一種專門用于碳纖、玻纖、復合材料的熱壓成型設備。整個成型過程需要嚴格控制溫度、壓力和成型時間等參數,以保證產品的質量和性能一致性。熱壓成型機采用伺服油路系統,低噪音,節能環保。獨特的發熱系統裝置,可分段、分區控制溫度和壓力,整體溫差可控制在±3度內,確保熱壓溫度的穩定性,大大提高產品的良率。
玻璃纖維(玻纖)熱壓成型工藝是制造玻纖增強塑料(GFRP)制品的核心工藝,通過高溫高壓將玻纖與樹脂結合,形成高強度、輕量化、耐腐蝕的復合材料結構。其關鍵工藝步驟、參數控制及技術難點如下:
一、核心工藝步驟
材料預處理與鋪層設計
玻纖材料選擇:
短切纖維(SMC/BMC):隨機分布,適合簡單形狀;
連續纖維預浸料:定向鋪層,可優化力學性能(如抗拉、抗彎)。
樹脂基體:
熱固性樹脂(如環氧樹脂、不飽和聚酯):固化后形成交聯網絡,耐高溫;
熱塑性樹脂(如PA、PP):可重復加工,環保性高,但需更高成型溫度。
鋪層設計:
根據力學需求設計纖維取向(單向、正交或角度鋪層),控制纖維體積分數(通常50%~65%)。
模具預熱與裝料
模具預熱:加熱至樹脂熔融溫度(熱固性:120~180°C;熱塑性:200~300°C),減少溫度梯度導致的殘余應力。
裝料方式:
預浸料裁剪后鋪疊;
干纖維+樹脂注射(如RTM工藝)需配合真空輔助。
加壓與浸潤階段
分階段加壓:
低壓階段(5~15 MPa):促進樹脂流動,充分浸潤纖維;
高壓階段(20~50 MPa):壓實材料,排出氣泡,降低孔隙率(目標<2%)。
真空輔助:結合真空系統(真空度<1 kPa),進一步消除孔隙。
固化/冷卻定型
熱固性樹脂:階梯升溫固化(如80°C→150°C→180°C),保溫保壓至樹脂完全交聯。
熱塑性樹脂:快速冷卻(水冷或風冷)定型,避免結晶度過高導致脆性。
脫模與后處理
脫模劑:使用硅基或氟聚合物脫模劑,減少粘連;
二次加工:CNC修邊、鉆孔、表面噴涂(如UV涂層)或功能化處理(導電鍍層)。
工藝原理
材料準備
將玻璃纖維與樹脂基體混合制成的預浸料,作為熱壓成型的基礎材料。預浸料中,玻璃纖維提供了高強度和剛性,樹脂則在加熱時能夠流動并固化,將玻璃纖維粘結在一起。
選擇合適的模具,其材質和設計需根據手機后蓋的尺寸、形狀和表面要求來確定,以確保產品精度和表面質量。
加熱階段
將裝有預浸料的模具放入熱壓機中,通過加熱系統對模具進行加熱。
加熱溫度通常根據樹脂基體的類型和固化特性來確定,一般在150℃-200℃之間。
加熱方式有電加熱、油加熱等,加熱過程中需確保模具內溫度均勻分布,可采用導熱油或電熱管加熱。
加壓階段
當模具溫度達到預設值后,啟動液壓系統或機械加壓裝置,向模具施加壓力。
壓力大小根據產品尺寸、厚度和樹脂含量等因素調整,一般在1-10MPa之間。
加壓過程中,預浸料在高溫和高壓作用下逐漸軟化、流動并填充模具型腔。
保溫保壓階段
保持模具的溫度和壓力一段時間,使樹脂充分固化。
保溫時間根據樹脂的固化特性確定,一般為幾分鐘到幾十分鐘不等。
在此階段,樹脂發生交聯反應,形成三維網狀結構,將玻璃纖維牢固地粘結在一起。
冷卻脫模階段
停止加熱,啟動冷卻系統對模具進行冷卻。
冷卻方式有自然冷卻、風冷、水冷等。
當模具溫度降至一定程度后,打開模具,取出成型后的玻纖手機后蓋產品。
工藝優勢
高精度
熱壓成型工藝通過精確的模具設計和溫度、壓力控制,能夠生產出尺寸精度高、形狀復雜的玻纖手機后蓋產品。
模具的精度和表面質量直接決定了產品的外觀和尺寸精度,可滿足手機后蓋與其他部件的裝配要求。
高性能
該工藝可使玻纖與樹脂充分結合,形成致密的復合材料結構,提高產品的強度、剛度和耐沖擊性。
通過合理選擇玻璃纖維的鋪設方式和樹脂基體,還可以賦予產品特定的性能,如電磁屏蔽、散熱等。
高效率
熱壓成型工藝具有較快的生產周期,能夠在短時間內完成產品的成型和固化。
相比于其他成型工藝,如手糊、模壓等,熱壓成型工藝的自動化程度較高,可大大提高生產效率。
靈活性
該工藝適用于各種類型和規格的玻纖手機后蓋生產,可通過更換模具和調整工藝參數來生產不同型號的產品。
還可實現多種顏色和紋理的設計,滿足不同消費者的需求。
工藝控制要點
溫度控制
這是熱壓成型工藝中的關鍵環節,直接影響樹脂的固化反應和產品質量。
需根據樹脂的類型和固化特性,制定合理的升溫曲線和保溫時間,確保樹脂充分固化,同時避免溫度過高導致樹脂分解或產品變形。
壓力控制
壓力的大小和均勻性對產品的密度、強度和表面質量有重要影響。
應根據產品的尺寸、厚度和樹脂含量等因素調整壓力,并在加壓過程中保持壓力的穩定。
同時,要避免壓力過大導致模具損壞或產品產生缺陷。
時間控制
保溫時間和加壓時間的長短直接影響產品的固化程度和性能。
過短的時間可能導致樹脂固化不完全,降低產品的強度和穩定性;過長的時間則會增加生產成本和能耗。
因此,需根據產品的具體要求和工藝條件,合理控制保溫時間和加壓時間。
三、技術難點與解決方案
孔隙率控制
成因:樹脂流動性不足、揮發分殘留、纖維排布不均。
對策:
預抽真空(真空輔助成型);
優化樹脂黏度(添加稀釋劑或提高溫度);
分階段加壓(低壓浸潤+高壓壓實)。
纖維取向與變形
難點:鋪層錯位導致力學性能不達標。
對策:
使用自動鋪帶機(ATL)或模內傳感器監控鋪層精度;
模具設計補償纖維回彈(如過彎角度修正)。
表面質量缺陷
問題:樹脂富集區或纖維裸露。
對策:
優化模具表面光潔度(鏡面拋光);
調整樹脂流動路徑(導流槽設計)。
四、典型應用案例
汽車輕量化部件(引擎蓋、車門)
工藝參數:160°C/30 MPa/3分鐘(環氧樹脂SMC);
特點:纖維含量60%,孔隙率<1.5%,減重40%。
電子設備外殼(5G基站、筆記本電腦)
工藝優化:熱塑性玻纖(PA+30%玻纖),快速冷卻成型,表面直接噴涂金屬質感涂層。
家電結構件(洗衣機滾筒、空調支架)
低成本方案:BMC材料(短切玻纖+不飽和聚酯),高壓成型,周期短(<2分鐘)。
五、未來工藝發展趨勢
智能化工藝控制:
嵌入光纖傳感器實時監測溫度、壓力及固化度;
AI算法動態調整參數(如基于機器學習的缺陷預測)。
綠色制造技術:
生物基樹脂(如大豆油環氧)替代石油基產品;
玻纖回收技術(機械粉碎或熱解分離)。
高性能復合材料升級:
玻纖與碳纖維混雜(如表面層碳纖+芯層玻纖),平衡成本與性能;
納米改性樹脂(添加石墨烯、碳納米管)提升導電/導熱性。
玻纖熱壓成型工藝憑借其高性價比和成熟的技術體系,在汽車、電子、家電等領域持續占據重要地位。未來通過智能化與綠色化升級,將進一步拓展其在高端制造中的應用邊界。
相關資訊
推薦產品
最新資訊 News
聯系我們 Contact Us
-
聯系人:劉大軍
手 機:18138436465
電 話:0755-28365643
傳 真:0755-89636058
郵 箱:33434175@qq.com
地 址:深圳市龍崗區坪地街道六聯社區鵝公嶺西路6-12號
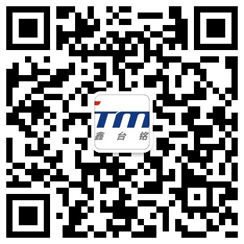