粉末伺服成型機:精密粉末制造的利器
鑫臺銘粉末伺服成型機:精密粉末制造的利器:---鑫臺銘提供。鑫臺銘---新智造走向世界!致力于3C電子、新能源、新材料產品成型及生產工藝解決方案。
粉末伺服成型機是一種先進的粉末成型設備,采用機、電、氣、儀一體化控制、伺服驅動技術,通過伺服馬達帶動絲桿轉動上沖、母模、下沖進行上下運動的粉末成型機。設備有獨立的伺服系統和電氣系統,具有浮動壓制,精確控制壓力和位移,實現了對精細粉末的高精度成型。設備智能精準、可配機械手、自動送粉+擺料。具有高產能、效果好、稼動率高等特點。
一、設備壓力:10T~1200T;
二、驅動方式:
1、上沖(伺服液壓缸驅動)+下沖(伺服液壓缸驅動);
2、上沖(伺服液壓缸驅動)+下沖(AC 伺服馬達+絲桿直連驅動);
3、上沖(AC 伺服馬達+絲桿直連驅動)+下沖(AC 伺服馬達+絲桿直連驅動);
三、模架結構:上一下一、上一下二、上一下三、上二下二、上二下三、上二下四;
四、精度要求:成型精度:≤0.02mm;重復精度:≤0.005mm
設備特點:
1、采用伺服馬達傳動,成型速度更快,穩定性更高,模具磨損低;
2、成品推出采用伺服馬達,填料更均勻,成品推出更順暢;
3、異型產品壓制成型后,產品拔出時,下型高出母型,機臺可設置粉盒推出延時裝置,粉盒與下型相接精準,可確保產品品質;
4、本設備智能化高,壓力自動監控,安全系數高;
5、本設備結構簡單,操作方便,保養容易;
6、本設備無需加液壓油,環保,節能。
粉末伺服成型機主要應用于硬質合金、粉末冶金、精密陶瓷、電子陶瓷、陶瓷結構件、電感磁芯、T-Core電感、銅鐵共燒電感、電感一體成型、磁性材料、磁環、鐵氧體、鐵硅鋁、玻璃、鐵基合金等粉末材料的壓制成型。產品應用于電感、半導體、通訊基站、變壓器、電源、3C電子、醫療、數控刀具、電動汽車、新能源(光伏、儲能、風電)等領域。
硬質合金:碳化鎢、氧化鎢、鎢粉...
陶瓷粉末:氧化鋁、氧化鋯、碳化硅、氧化硅...
磁性材料:錳鋅鐵氧體、鎳鋅鐵氧體、釹鐵硼、鋁鐵硼、鐵硅、鐵硅鋁、合金粉、鐵粉...
在精密制造領域,粉末伺服成型機憑借其納米級控制精度、復雜結構成型能力及全流程智能化,已成為金屬、陶瓷、復合材料等高端粉末制品生產的核心裝備。從微米級電子元件到高性能醫療器械,它通過數字化工藝革新,重新定義了粉末成型的技術邊界。以下從技術內核、核心優勢、行業應用及未來潛力,解析其為何被譽為精密粉末制造的“終極利器”。
一、技術內核:數字化與力控的完美融合
閉環伺服驅動系統
三軸精密控制:X/Y/Z軸獨立伺服電機驅動,配合高精度滾珠絲杠,實現位移精度±0.001mm,壓力波動≤0.5%。
多段動態壓制:支持10段以上壓力-位移曲線編程,適應材料壓縮比變化(如金屬粉末從松散態到致密態的梯度加壓)。
智能傳感與反饋
實時壓力補償:通過應變片或壓電傳感器,動態修正模具彈性變形(尤其在硬質合金壓制中,補償量可達0.02-0.05mm)。
溫度同步監控:集成紅外測溫模塊,確保溫壓成型時模具溫度均勻性(±2℃以內)。
模塊化設計
快速換模系統:液壓鎖緊+定位銷設計,模具切換時間≤5分鐘,適配多品種小批量生產。
可擴展功能單元:按需集成真空除氣、超聲波振動輔助填充、激光在線檢測等模塊。
伺服電機驅動與精確控制
粉末伺服成型機的核心在于其先進的伺服電機驅動系統。伺服電機能夠根據預設的程序和指令,精確地控制壓力、位移和速度等參數。在粉末成型過程中,壓力控制的精度至關重要。例如,在一些高精度電子元件的粉末壓制中,壓力控制精度可以達到±0.3%以內。
位移控制同樣精準,伺服電機通過脈沖編碼器等裝置,能夠精確地控制模具的開合程度。對于需要嚴格控制尺寸精度的小型精密零件,如微型齒輪、精密傳感器外殼等,位移控制的精度可以達到微米級別。這使得成型后的零件尺寸準確,符合高精度制造的要求。
先進的模具設計與配合
精密的模具設計是粉末伺服成型機實現精密成型的關鍵因素之一。模具通常采用高強度、高硬度的合金材料制成,以保證在高壓下不變形。同時,模具的型腔加工精度非常高,表面粗糙度可以達到Ra0.8以下。
模具與粉末伺服成型機的配合也經過精心設計。模具的安裝和定位采用高精度的導向裝置,確保在成型過程中模具的位置準確無誤。在成型時,模具與粉末之間的間隙均勻一致,保證了粉末在成型過程中受到的壓力均勻分布,從而提高了零件的成型精度。
二、核心優勢:精密制造的突破性提升
微米級成型精度
尺寸公差控制:重復定位精度±0.005mm,適合微型零件(如直徑0.5mm的陶瓷插芯、厚度0.2mm的金屬密封片)。
表面光潔度優化:通過精壓階段微米級位移控制,生坯表面粗糙度Ra≤0.4μm,減少后續研磨成本。
復雜結構一體化成型
多臺階/異形腔體:通過多工位模架與程序化分段壓制,實現齒輪、渦輪葉片等復雜結構一次成型。
薄壁與鏤空設計:支持壁厚0.3mm以下的微型結構(如MEMS傳感器殼體),良率提升至95%以上。
材料適應性與性能優化
超細粉末成型:針對粒徑≤10μm的納米碳化鎢、氧化鋯等材料,通過低頻振動輔助填充,密度均勻性>99%。
梯度材料制備:通過層疊壓制技術,實現金屬-陶瓷復合材料的界面無縫結合(如航天耐熱部件)。
全流程智能化管理
工藝參數自學習:AI算法分析歷史數據,自動推薦最優壓制曲線,試模周期縮短50%。
生產追溯系統:每件生坯附帶數字孿生檔案(壓力、溫度、位移數據),支持質量溯源與工藝優化。
選型關鍵:匹配精密制造的極致需求
精度等級選擇
工業級(±0.02mm):通用型零件(如汽車齒輪、磁性元件)。
超精密級(±0.005mm):光學、醫療、軍工等高附加值領域。
功能模塊定制
真空除氣系統:硬質合金、陶瓷等氣敏材料必備,真空度≤10Pa。
溫控模架:加熱范圍50-300℃,適配溫壓成型(如PEEK高分子粉末)。
在線檢測單元:集成激光測厚、CCD視覺檢測,實時剔除不良品。
智能化配置
物聯網(IoT)接口:與MES/ERP系統對接,實現生產數據云端管理。
數字孿生平臺:虛擬調試與工藝仿真,降低試產風險。
對材料適應性的精密體現
金屬粉末的精細成型
對于各種金屬粉末,如貴金屬粉末(金、銀、鉑等)和非貴金屬粉末(鐵、銅、鋁等),粉末伺服成型機都能夠實現精細成型。以貴金屬粉末為例,在制造珠寶首飾或高精度電子元件引腳時,需要精確控制粉末的用量和成型厚度。
伺服粉末成型機可以通過精確的壓力和位移控制,將貴金屬粉末壓制成所需的形狀和尺寸。在成型過程中,還可以根據不同的金屬材料特性,調整成型參數,如壓力大小、保壓時間和成型溫度等。對于軟金屬粉末,可以采用較低的壓力和較短的保壓時間,避免材料過度變形;對于硬金屬粉末,則可以適當增加壓力和保壓時間,以提高零件的密度和強度。
特殊復合材料的精密制造
除了純金屬粉末,粉末伺服成型機還適用于各種特殊復合材料的精密制造。例如,陶瓷 - 金屬復合材料在電子封裝領域有廣泛應用。這種材料結合了陶瓷的高絕緣性和金屬的良好導熱性。
伺服粉末成型機能夠將陶瓷粉末和金屬粉末按照精確的比例混合后進行成型。通過精確控制成型過程中的壓力和位移,使兩種材料的顆粒均勻分布,形成具有優異性能的復合材料零件。同時,對于一些含有稀土元素的復合材料,伺服粉末成型機也可以準確地控制稀土元素的分布,提高零件的特殊性能。
結語
粉末伺服成型機不僅是精密制造的“工具進化”,更是材料科學與數字技術深度融合的產物。其通過精度躍遷、復雜結構解放與智能化升級,正在推動航空航天、生物醫療、高端電子等領域的顛覆性創新。對于企業而言,掌握這一“利器”,即意味著在精密制造賽道中搶占技術制高點,實現從“跟跑”到“領跑”的關鍵跨越。未來,隨著超精密加工與AI的深度結合,粉末伺服成型機的潛力將遠超想象——它不僅是制造的利器,更是開啟微觀世界無限可能的鑰匙。
相關資訊
推薦產品
最新資訊 News
聯系我們 Contact Us
-
聯系人:劉大軍
手 機:18138436465
電 話:0755-28365643
傳 真:0755-89636058
郵 箱:33434175@qq.com
地 址:深圳市龍崗區坪地街道六聯社區鵝公嶺西路6-12號
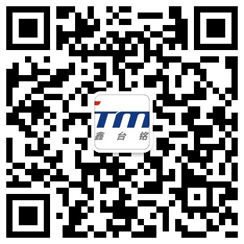